基于Industrial IT控制系統實現專家優化控制功能
DCS控制系統實現了全廠范圍的自動化控制,幾乎所有的企業決策者都能夠主動選擇一套DCS系統控制其生產線,而專家優化系統并不被企業決策者所重視,但隨著專家優化系統的不斷引入,其作用將逐漸顯現出來。
從控制功能上看,DCS系統解決了常規對象的控制問題,而對于復雜的被控對象,其不確定性、非線性以及非精確性對于DCS控制系統和對生產工藝及設備知之不多的自動化工程師是一個難題,而專家優化系統可以解決這一問題。專家優化系統是由生產工藝專家、生產設備專家和自動化控制專家共同研發的,是融入了專家經驗和現代控制技術的智能系統,專家優化控制系統包括專家控制、多模式控制和自校正PID控制等工作方式。
Industrial IT控制系統
Industrial IT是ABB公司的控制系統,它使工業技術和信息技術相結合,構建了以屬性目標平臺為基礎的、開放的應用系統。Industrial IT不僅提供控制功能,而且是貫穿企業生產、管理、決策等行為的工作平臺。
Industrial IT的系統結構參見Industrial IT系統結構圖(見圖1)。
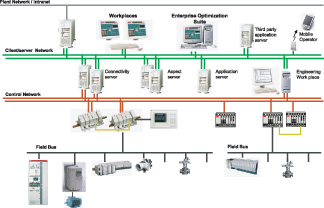
圖1: Industrial IT系統結構圖
根據專家優化系統對Industrial IT系統硬件要求的不同,專家優化系統可以完全集成到Industrial IT系統的硬件之中,把優化程序集成到控制器中,利用工程師站及操作員站進行組態、調試和操作;專家優化系統也可以獨立配置一套SERVER/CLIENT結構,增加一個Application Server作為專家優化系統的服務器,增加幾臺Workplace作為專家優化系統的工作站。ACC系統和EO系統是兩套應用于不同過程控制的專家優化系統,ACC系統完全集成到Industrial IT控制系統之中進行工作;EO系統獨立配置一套SERVER/CLIENT硬件結構。
自動燃燒控制系統(ACC)
自動燃燒控制系統(ACC)是由TAKUMA公司為爐排式垃圾燃燒爐的控制而研制的燃燒優化控制系統,其目的是保持燃燒穩定、高效利用能源。自動燃燒控制系統(ACC)的主要任務是獲得穩定的蒸汽量,同時,嚴格控制廢氣中的氧含量,需要同時調節一次風量、二次風量、喂料速度和爐排速度。
自動燃燒控制系統(ACC)由蒸汽流量控制子系統、爐排速度控制子系統、燃燒用空氣流量控制子系統和氧含量控制子系統構成。
蒸汽流量控制子系統
垃圾燃料的質量即其卡路里含量受時間和季節的影響很大,燃燒過程中通過調節燃燒用空氣流量以及每段爐排的速度來減小垃圾燃料熱量的波動,穩定爐膛溫度、蒸汽流量、日處理垃圾數量并控制飛灰質量。
蒸汽流量控制可以通過最小化燃燒波動的方法來實現,當垃圾燃料熱值變化時,要求投入適量的燃燒用空氣到爐膛,同時保證適量的垃圾燃料在燃燒區域。
目標蒸汽流量是由操作員設定的,燃燒用空氣流量的計算是在設定目標蒸汽流量值和目標氧含量值的基礎上自動計算出來的。然后,根據蒸汽流量值、燃燒用空氣流量值計算出爐排速度值。
因此,蒸汽流量控制是通過爐排速度控制和燃燒用空氣流量控制來實現的。
爐排速度控制
爐排速度的控制有手動方式和自動方式,在手動方式下,操作員可以直接設定速度。在自動方式下,目標速度的設定來自于ACC程序。在完成調試之后,每段爐排的速度基本上是不變的,其整定值在調試期間確定。
燃燒段爐排的速度是根據目標蒸汽流量和實際流量與目標流量的偏差校正計算之后得到的。另外,該速度也受控于空氣與燃料之比和燃盡段傳感器的測量值。
燃燒段爐排的燃燒波動是由專用傳感器檢測的,如果燃盡段的燃燒波動是由于垃圾燃料質量的大幅度變化或由于其他極端條件引起的,為防止增加未燃盡的垃圾量,燃燒爐排的速度將被減慢。
干燥段爐排的速度基本上與燃燒段爐排的速度成正比例,同時也受垃圾料層厚度值的修正,垃圾料位開關位于燃燒段的上部,用于檢測垃圾層厚度,同時用于校對干燥段爐排的速度,保證料層厚度不變。
進料器速度基本上與干燥段爐排的速度成正比例,同時也受料層厚度修正。
ACC不控制燃盡段的爐排速度。其速度是一個常量值,并且操作員可以根據飛灰條件改變該值。
燃燒用空氣流量控制子系統
必要的燃燒用空氣流量是根據目標蒸汽流量和規定的氧含量值計算得到的。一次風和二次風被適當地分配到每一個爐排。其分配比例在調試整定之后基本不變。燃燒用空氣流量的控制有手動方式、自動方式以及串級控制方式。操作員在手動方式下可以直接打開控制空氣的擋板到一定位置;在自動控制方式下,操作員可以根據目標流量控制空氣流量為一個常量;在串級控制方式下,目標空氣流量值由ACC設定。二次風空氣流量通過含氧量和爐膛煙氣溫度值進行補償。
ACC系統與Industrial IT控制器的集成
圖2為Industrial IT系統組態的界面,ACC系統的算法成為控制器的一個任務,它將隨著其他程序一起下裝到控制器之中,即ACC系統嵌入到了Industrial IT系統。
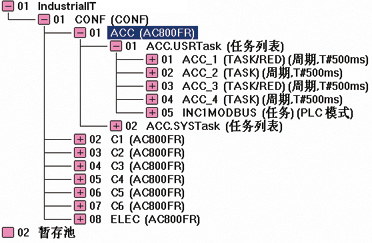
圖2:Industrial IT系統組態界面
EO系統
EO系統是由ABB公司研發、廣泛應用于工業窯爐控制及工業粉磨機控制的專家優化系統。EO系統包含了人工智能控制算法(AI)及基于模型的控制算法(MBC),控制策略的組態使用模糊邏輯控制、神經元網絡控制和模型預估控制等算法完成。EO系統可以明顯提高生產效率,通過最佳的控制策略,保證生產的穩定性。
EO系統應用于干法水泥生產窯
EO系統的應用可以提高熟料的產量、提高熟料的質量、改善熟料的穩定性、減少廢氣、廢料的排放量,同時降低 3- 7%的熱能消耗。參見圖3水泥生產窯工作示意圖。
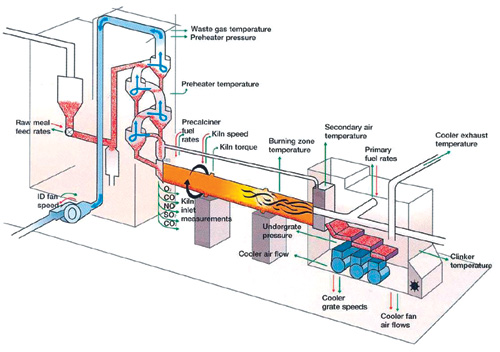
圖3:水泥生產窯工作示意圖
EO系統從Industrial IT控制系統采集的變量包括:預熱器氧含量、預熱器溫度、一氧化碳濃度、窯入口溫度、窯出口溫度、分解段溫度和窯主傳電機電流等。
EO系統完成計算后輸出到Industrial IT系統的控制變量有:引風機速度、窯喂料量、窯轉速和噴煤(
油)量等。
EO系統的組態和調試
EO系統一般是由工藝工程師進行控制策略的組態,EO提供的組態界面是圖形化界面,不是傳統的基于文本的環境,使工藝工程師能夠迅速掌握組態方法。EO系統的調試一般需要兩次完成,第一次調試在系統完成安裝之后就可以開始,通常需要5周時間。第二次調試在熟料生產3個月以后就可以開始,通常需要5周時間完成控制策略的精確調試。EO系統也可以應用在沒有采用優化控制的舊生產線上。
Industrial IT控制系統具有良好的接口能力,可以方便地與各種專家優化系統集成為一體,并且有多種集成方法,在Industrial IT控制系統的基礎上實現優化控制的項目不斷出現。在大中型控制系統中,選擇“DCS系統+專家優化系統”控制模式的比例逐年上升。專家優化系統的作用將逐漸顯現出來,必將被越來越多的企業決策者選用。
CS控制系統實現了全廠范圍的自動化控制,幾乎所有的企業決策者都能夠主動選擇一套DCS系統控制其生產線,而專家優化系統并不被企業決策者所重視,但隨著專家優化系統的不斷引入,其作用將逐漸顯現出來。
從控制功能上看,DCS系統解決了常規對象的控制問題,而對于復雜的被控對象,其不確定性、非線性以及非精確性對于DCS控制系統和對生產工藝及設備知之不多的自動化工程師是一個難題,而專家優化系統可以解決這一問題。專家優化系統是由生產工藝專家、生產設備專家和自動化控制專家共同研發的,是融入了專家經驗和現代控制技術的智能系統,專家優化控制系統包括專家控制、多模式控制和自校正PID控制等工作方式。
Industrial IT控制系統
Industrial IT是ABB公司的控制系統,它使工業技術和信息技術相結合,構建了以屬性目標平臺為基礎的、開放的應用系統。Industrial IT不僅提供控制功能,而且是貫穿企業生產、管理、決策等行為的工作平臺。
Industrial IT的系統結構參見Industrial IT系統結構圖(見圖1)。
根據專家優化系統對Industrial IT系統硬件要求的不同,專家優化系統可以完全集成到Industrial IT系統的硬件之中,把優化程序集成到控制器中,利用工程師站及操作員站進行組態、調試和操作;專家優化系統也可以獨立配置一套SERVER/CLIENT結構,增加一個Application Server作為專家優化系統的服務器,增加幾臺Workplace作為專家優化系統的工作站。ACC系統和EO系統是兩套應用于不同過程控制的專家優化系統,ACC系統完全集成到Industrial IT控制系統之中進行工作;EO系統獨立配置一套SERVER/CLIENT硬件結構。
自動燃燒控制系統(ACC)
自動燃燒控制系統(ACC)是由TAKUMA公司為爐排式垃圾燃燒爐的控制而研制的燃燒優化控制系統,其目的是保持燃燒穩定、高效利用能源。自動燃燒控制系統(ACC)的主要任務是獲得穩定的蒸汽量,同時,嚴格控制廢氣中的氧含量,需要同時調節一次風量、二次風量、喂料速度和爐排速度。
自動燃燒控制系統(ACC)由蒸汽流量控制子系
從控制功能上看,DCS系統解決了常規對象的控制問題,而對于復雜的被控對象,其不確定性、非線性以及非精確性對于DCS控制系統和對生產工藝及設備知之不多的自動化工程師是一個難題,而專家優化系統可以解決這一問題。專家優化系統是由生產工藝專家、生產設備專家和自動化控制專家共同研發的,是融入了專家經驗和現代控制技術的智能系統,專家優化控制系統包括專家控制、多模式控制和自校正PID控制等工作方式。
Industrial IT控制系統
Industrial IT是ABB公司的控制系統,它使工業技術和信息技術相結合,構建了以屬性目標平臺為基礎的、開放的應用系統。Industrial IT不僅提供控制功能,而且是貫穿企業生產、管理、決策等行為的工作平臺。
Industrial IT的系統結構參見Industrial IT系統結構圖(見圖1)。
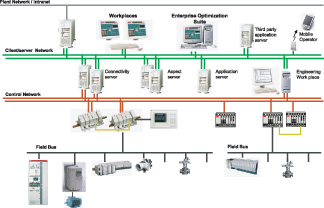
圖1: Industrial IT系統結構圖
根據專家優化系統對Industrial IT系統硬件要求的不同,專家優化系統可以完全集成到Industrial IT系統的硬件之中,把優化程序集成到控制器中,利用工程師站及操作員站進行組態、調試和操作;專家優化系統也可以獨立配置一套SERVER/CLIENT結構,增加一個Application Server作為專家優化系統的服務器,增加幾臺Workplace作為專家優化系統的工作站。ACC系統和EO系統是兩套應用于不同過程控制的專家優化系統,ACC系統完全集成到Industrial IT控制系統之中進行工作;EO系統獨立配置一套SERVER/CLIENT硬件結構。
自動燃燒控制系統(ACC)
自動燃燒控制系統(ACC)是由TAKUMA公司為爐排式垃圾燃燒爐的控制而研制的燃燒優化控制系統,其目的是保持燃燒穩定、高效利用能源。自動燃燒控制系統(ACC)的主要任務是獲得穩定的蒸汽量,同時,嚴格控制廢氣中的氧含量,需要同時調節一次風量、二次風量、喂料速度和爐排速度。
自動燃燒控制系統(ACC)由蒸汽流量控制子系統、爐排速度控制子系統、燃燒用空氣流量控制子系統和氧含量控制子系統構成。
蒸汽流量控制子系統
垃圾燃料的質量即其卡路里含量受時間和季節的影響很大,燃燒過程中通過調節燃燒用空氣流量以及每段爐排的速度來減小垃圾燃料熱量的波動,穩定爐膛溫度、蒸汽流量、日處理垃圾數量并控制飛灰質量。
蒸汽流量控制可以通過最小化燃燒波動的方法來實現,當垃圾燃料熱值變化時,要求投入適量的燃燒用空氣到爐膛,同時保證適量的垃圾燃料在燃燒區域。
目標蒸汽流量是由操作員設定的,燃燒用空氣流量的計算是在設定目標蒸汽流量值和目標氧含量值的基礎上自動計算出來的。然后,根據蒸汽流量值、燃燒用空氣流量值計算出爐排速度值。
因此,蒸汽流量控制是通過爐排速度控制和燃燒用空氣流量控制來實現的。
爐排速度控制
爐排速度的控制有手動方式和自動方式,在手動方式下,操作員可以直接設定速度。在自動方式下,目標速度的設定來自于ACC程序。在完成調試之后,每段爐排的速度基本上是不變的,其整定值在調試期間確定。
燃燒段爐排的速度是根據目標蒸汽流量和實際流量與目標流量的偏差校正計算之后得到的。另外,該速度也受控于空氣與燃料之比和燃盡段傳感器的測量值。
燃燒段爐排的燃燒波動是由專用傳感器檢測的,如果燃盡段的燃燒波動是由于垃圾燃料質量的大幅度變化或由于其他極端條件引起的,為防止增加未燃盡的垃圾量,燃燒爐排的速度將被減慢。
干燥段爐排的速度基本上與燃燒段爐排的速度成正比例,同時也受垃圾料層厚度值的修正,垃圾料位開關位于燃燒段的上部,用于檢測垃圾層厚度,同時用于校對干燥段爐排的速度,保證料層厚度不變。
進料器速度基本上與干燥段爐排的速度成正比例,同時也受料層厚度修正。
ACC不控制燃盡段的爐排速度。其速度是一個常量值,并且操作員可以根據飛灰條件改變該值。
燃燒用空氣流量控制子系統
必要的燃燒用空氣流量是根據目標蒸汽流量和規定的氧含量值計算得到的。一次風和二次風被適當地分配到每一個爐排。其分配比例在調試整定之后基本不變。燃燒用空氣流量的控制有手動方式、自動方式以及串級控制方式。操作員在手動方式下可以直接打開控制空氣的擋板到一定位置;在自動控制方式下,操作員可以根據目標流量控制空氣流量為一個常量;在串級控制方式下,目標空氣流量值由ACC設定。二次風空氣流量通過含氧量和爐膛煙氣溫度值進行補償。
ACC系統與Industrial IT控制器的集成
圖2為Industrial IT系統組態的界面,ACC系統的算法成為控制器的一個任務,它將隨著其他程序一起下裝到控制器之中,即ACC系統嵌入到了Industrial IT系統。
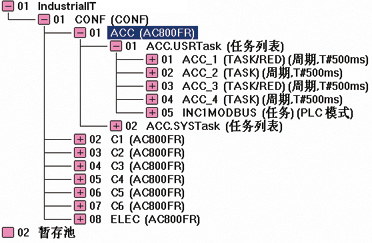
圖2:Industrial IT系統組態界面
EO系統
EO系統是由ABB公司研發、廣泛應用于工業窯爐控制及工業粉磨機控制的專家優化系統。EO系統包含了人工智能控制算法(AI)及基于模型的控制算法(MBC),控制策略的組態使用模糊邏輯控制、神經元網絡控制和模型預估控制等算法完成。EO系統可以明顯提高生產效率,通過最佳的控制策略,保證生產的穩定性。
EO系統應用于干法水泥生產窯
EO系統的應用可以提高熟料的產量、提高熟料的質量、改善熟料的穩定性、減少廢氣、廢料的排放量,同時降低 3- 7%的熱能消耗。參見圖3水泥生產窯工作示意圖。
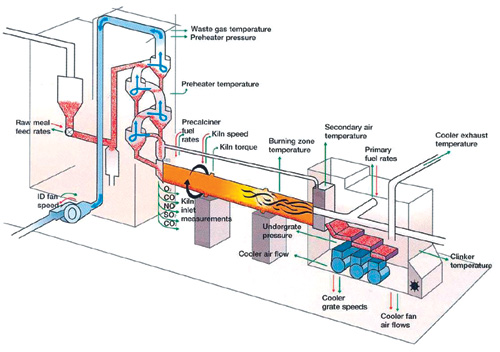
圖3:水泥生產窯工作示意圖
EO系統從Industrial IT控制系統采集的變量包括:預熱器氧含量、預熱器溫度、一氧化碳濃度、窯入口溫度、窯出口溫度、分解段溫度和窯主傳電機電流等。
EO系統完成計算后輸出到Industrial IT系統的控制變量有:引風機速度、窯喂料量、窯轉速和噴煤(
EO系統的組態和調試
EO系統一般是由工藝工程師進行控制策略的組態,EO提供的組態界面是圖形化界面,不是傳統的基于文本的環境,使工藝工程師能夠迅速掌握組態方法。EO系統的調試一般需要兩次完成,第一次調試在系統完成安裝之后就可以開始,通常需要5周時間。第二次調試在熟料生產3個月以后就可以開始,通常需要5周時間完成控制策略的精確調試。EO系統也可以應用在沒有采用優化控制的舊生產線上。
Industrial IT控制系統具有良好的接口能力,可以方便地與各種專家優化系統集成為一體,并且有多種集成方法,在Industrial IT控制系統的基礎上實現優化控制的項目不斷出現。在大中型控制系統中,選擇“DCS系統+專家優化系統”控制模式的比例逐年上升。專家優化系統的作用將逐漸顯現出來,必將被越來越多的企業決策者選用。
CS控制系統實現了全廠范圍的自動化控制,幾乎所有的企業決策者都能夠主動選擇一套DCS系統控制其生產線,而專家優化系統并不被企業決策者所重視,但隨著專家優化系統的不斷引入,其作用將逐漸顯現出來。
從控制功能上看,DCS系統解決了常規對象的控制問題,而對于復雜的被控對象,其不確定性、非線性以及非精確性對于DCS控制系統和對生產工藝及設備知之不多的自動化工程師是一個難題,而專家優化系統可以解決這一問題。專家優化系統是由生產工藝專家、生產設備專家和自動化控制專家共同研發的,是融入了專家經驗和現代控制技術的智能系統,專家優化控制系統包括專家控制、多模式控制和自校正PID控制等工作方式。
Industrial IT控制系統
Industrial IT是ABB公司的控制系統,它使工業技術和信息技術相結合,構建了以屬性目標平臺為基礎的、開放的應用系統。Industrial IT不僅提供控制功能,而且是貫穿企業生產、管理、決策等行為的工作平臺。
Industrial IT的系統結構參見Industrial IT系統結構圖(見圖1)。
根據專家優化系統對Industrial IT系統硬件要求的不同,專家優化系統可以完全集成到Industrial IT系統的硬件之中,把優化程序集成到控制器中,利用工程師站及操作員站進行組態、調試和操作;專家優化系統也可以獨立配置一套SERVER/CLIENT結構,增加一個Application Server作為專家優化系統的服務器,增加幾臺Workplace作為專家優化系統的工作站。ACC系統和EO系統是兩套應用于不同過程控制的專家優化系統,ACC系統完全集成到Industrial IT控制系統之中進行工作;EO系統獨立配置一套SERVER/CLIENT硬件結構。
自動燃燒控制系統(ACC)
自動燃燒控制系統(ACC)是由TAKUMA公司為爐排式垃圾燃燒爐的控制而研制的燃燒優化控制系統,其目的是保持燃燒穩定、高效利用能源。自動燃燒控制系統(ACC)的主要任務是獲得穩定的蒸汽量,同時,嚴格控制廢氣中的氧含量,需要同時調節一次風量、二次風量、喂料速度和爐排速度。
自動燃燒控制系統(ACC)由蒸汽流量控制子系
文章版權歸西部工控xbgk所有,未經許可不得轉載。
上一篇:研祥EIP在商業領域的應用
下一篇:現場總線與DCS的網絡集成